Using plasma technology to recycle CO₂ from steelmaking
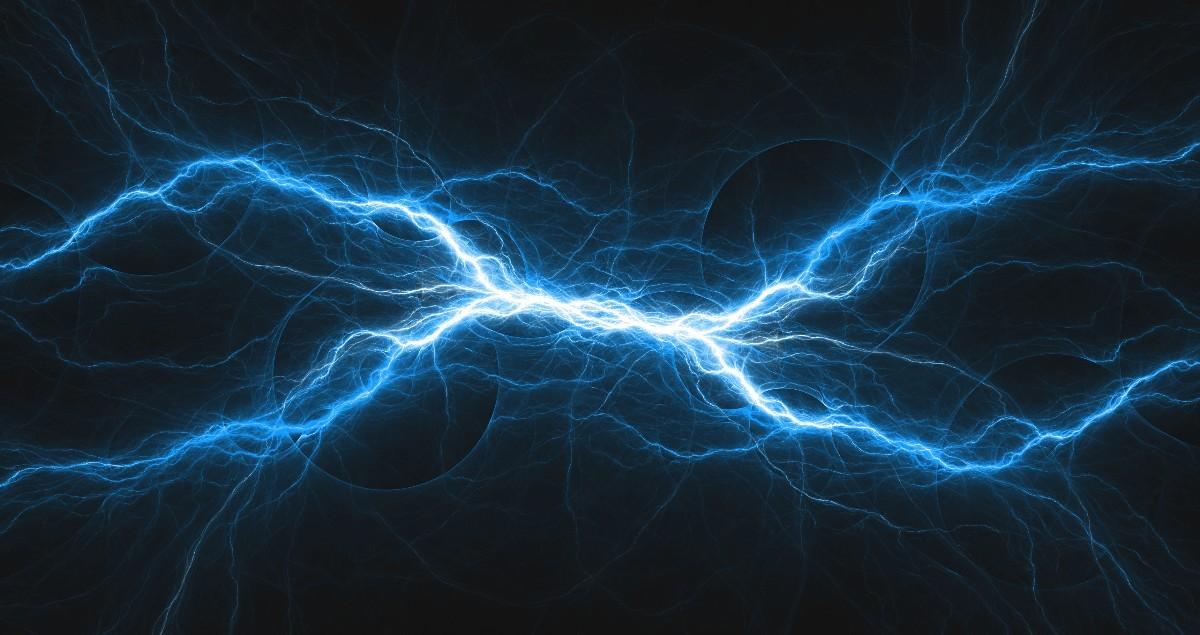
Plasma is all around us, comprising 99% of the visible universe, including the stars at night and the branch of lightning we see cracking open the sky.
Researchers are using the power of this superheated matter for everything from making computer chips to healing wounds. And in Belgium, three companies are collaborating on a world-first technology: a plasma reactor that turns captured CO₂ into carbon monoxide (CO) for steel and chemical production.
The process holds promise for decarbonizing steelmaking.
The role of CO₂ recycling
The steel sector creates more CO₂ than any other heavy industry and is considered challenging to electrify. This is because traditional steelmaking in blast furnaces uses coal as both a source of heat and, in the chemical process, as a reductant for converting iron ore to elemental (‘pig’) iron.
While the sector looks to future-proof with technologies such as electric arc furnaces and direct reduction of iron ore with hydrogen, it is looking to CO₂ capture, utilization and storage to help decarbonize existing assets.
At steelmaker ArcelorMittal’s site in Gent, Belgium, teams of engineers are working on a unique initiative in this space. The trial is capturing CO₂ from the plant, via a carbon capture unit from Mitsubishi Heavy Industries (MHI) Group and recycling it into CO. This can then be fed back into the process to replace coal as a reductant.
An ‘exciting’ process
The conversion to CO happens in a plasma reactor from Belgium-based climate technology company D-CRBN.
Traditional processes for splitting CO₂ into CO and oxygen require very high temperatures to spark the chemical reactions that separate the carbon dioxide molecules. These methods are energy-intensive and typically powered by fossil fuels. D-CRBN has devised a fully electrified process instead. Its plasma reactor can use renewable electricity to split CO₂ captured from the off-gases at Arcelor Mittal’s blast furnace. The resulting oxygen is consumed in the process, helping to boost the reactor’s efficiency. The carbon monoxide subsequently becomes a feedstock in the steelmaking process.
“We all know plasma,” says Gill Scheltjens, CEO at D-CRBN, a chemical engineer with a PhD in plasma technology. “If you unplug a power cord very fast, you see a spark. Basically, we are doing the same but in a CO₂ atmosphere. In that spark, electricity is being pushed through the molecules so they are excited to such an extent that they fall apart.”
Breaking this bond through a fully electrified process is one of the big advantages of D-CRBN’s technology, Scheltjens says. “In terms of electrification of chemical processes, this is a huge step forward.”
A promising solution for decarbonizing steel
It could also prove to be a significant step forward for steelmaking, and Scheltjens describes the trial at ArcelorMittal Gent as a “miniature version of what we want to do in the future”.
In summer 2024, a pipeline between MHI's carbon capture unit and D-CRBN's unit was connected to test the feasibility of using the captured CO₂ as a feedstock for D-CRBN’s technology. This is a key stage of testing, to ensure that any impurities that accompany the CO₂ produced during steelmaking do not have a detrimental effect on the process.
“Everything that’s put into our plasma reactor will come out, but shuffled,” Scheltjens explains. “So, the purer the feed stream, the easier it is to transform the CO₂ into CO. The advantage of working with MHI is that we receive a very pure CO₂ stream.”
Putting captured CO₂ to use
From this industrial pilot, D-CRBN’s aim is to scale the technology to convert 1 million tonnes of CO₂ a year — equivalent to the annual amount emitted by a typical blast furnace, Scheltjens says.
For MHI, the collaboration provides another addition to its suite of solutions for decarbonizing the steel industry, each of which could solve problems for different businesses or regions. As Florian Möllenbruck, Head of the Project Engineering Team at MHI, says: “There are locations that are favorable for storing CO₂, but conversion is also a big topic and this technology could play an essential role for the steel industry.
“Not only can it create a feedstock for steelmaking itself, but by adding hydrogen we can make syngas, which can serve as a feedstock for multiple applications, for instance the production of ethanol, methanol and sustainable aviation fuels. There’s almost no limitation to the potential market application.”
Website: ac.sciencefather.com
Nomination link:
https://academicawards.sciencefather.com/award-nomination/?ecategory=Awards&rcategory=Awardee
Nomination link:
https://academicawards.sciencefather.com/award-nomination/?ecategory=Awards&rcategory=Awardee
Contact us: academic@sciencefather.com
Get connected Here:
Facebook: https://www.facebook.com/profile.php?id=100093671170511Instagram: https://www.youtube.com/channel/UCM-OlZD0B3uvxFE2dEITMhg
Linkedin: https://www.linkedin.com/in/harita-r-1b9861224/
YouTube: https://www.youtube.com/channel/UCM-OlZD0B3uvxFE2dEITMhg
#academicawards #sciencefather #scientists #researcher #analysts #cybersecurity #plantcells #animalcells #hybridcells #plasmatechnology#co₂recycling #steelmakinginnovation #sustainablemetals #carbondioxidecapture #greensteel #climatetechnology #cleanenergytech #circulareconomy #emissionsreduction #industrialdecarbonization #renewablemetallurgy #carbonutilization #lowemissionssteel #netzerotechnology #plasmagasification #co₂utilization
Comments
Post a Comment